You have decided to turn that empty storage building into a metalworking shop. That's a great idea! And if you have experience operating most of the equipment that will go into the workshop, the most challenging part should be planning it.
You have two options: You can either place your equipment in what seems like a good location and move it later when you discover otherwise or arrange it correctly from the start.
Since we are suggesting you take the latter approach, here are a few tips to help you get it right the first time:
Write down the types of projects you intend to take on
Maybe you are a skilled welder and want to do fabrication work, or perhaps you have a list of round projects that will require a metal lathe. The equipment and tools you purchase, along with your workshop's floorplan, will depend primarily on the type of work you have in mind.
Assuming that you will revolve your work mostly around fabrication-type projects, here is what you will need and some things to consider as you plan your new workshop:
Start with a saw
It's hard to imagine a workshop without a saw to cut metal, so make it the cornerstone of your new shop. You will have three types from which to choose:
- A cold saw is a circular metal saw that provides accurate and clean cuts right from the machine. You can avoid secondary operations, such as deburring and grinding, with a cold saw.
Cold Saw
- The horizontal bandsaw is a versatile saw that can handle relatively large pieces. You can set it to cut automatically, freeing you up for other tasks. Horizontal bandsaws are available in stationary, portable, and benchtop models.
Horizontal Bandsaw
- Vertical bandsaws work well if you are cutting complex shapes or angles. Unlike the horizontal saw, however, you cannot clamp the stock you are cutting, increasing the injury risk.
Vertical Bandsaw –
As you plan your workshop, keep in mind that you must consider the saw's dimensions and have room for an operator. While you can position the saw with its back against a wall, you must leave areas on either side of the saw for cutting long pieces of bar stock.
The essential drill press and vise
You might be able to get away with just a hand drill if you are working with wood or other softer materials, but if you are going to be drilling into metal, you need a drill press in your new workshop. Even if you are only drilling the occasional hole, you will be thankful for it the first time you are required to drill a ½" diameter hole into a thick piece of carbon steel.
Drill presses also come in either benchtop or floor models that take up little floor space in your shop's layout. Although you will use the drill press predominately drilling holes, you can also use these versatile machines for enlarging existing holes, boring or reaming precision holes, and tapping threaded holes.
Hold your work securely with a drill press vise. Buy one that has a heavy cast body and opens to 3" or more. Most quality vises will have a v-notch in the solid jaw for holding round pieces.
Drill Press
A belt grinder should be part of every metalworking shop
At some point, you will need to break an edge, add an outside corner radius, smooth a rough surface, or remove a bit of material from the end of a metal bar. You can't do any of those things efficiently with a file, a hand grinder, or even a belt sander. Save yourself from unnecessary frustration and choose a belt grinder that was designed for metalworking.
The belt speed on the grinder is approximately twice that of the sander so that you can remove more metal in less time. Belt grinders have more than one contact point, usually against the platen or where the belt travels across the fixed contact wheel.
Belt Grinder
You might want to consider an arbor press
If you ever have a time when you need to exert slow, steady pressure—driving in press-fit bearings, for instance—you will be glad you added an arbor press to your workshop.
Metalworkers find all sorts of uses for these simple but powerful tools. In addition to pressing bearings in and out, they work well for punching holes, setting rivets, bending metal into various shapes, and even reloading ammunition.
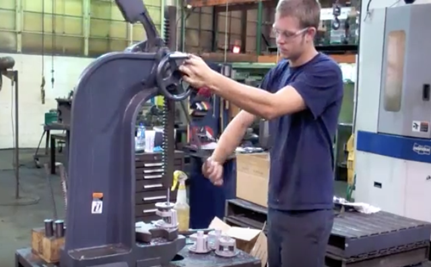
A hydraulic press can help you with those small and larger jobs
As you plan your workshop, be mindful of the opportunities for additional work that each piece of equipment opens for you.
For instance, if you are thinking about pursuing automotive repairs involving replacing bushings, bearings, universal joints, and pulleys, a hydraulic press for forcing components apart and replacing them could give you another avenue of income.
Photo Credit: ID Tools
If automotive work isn't on your agenda, consider all the other uses for these powerful machines: broaching keyways, straightening metal parts, press fits, assembly, punching, and an almost endless list of similar applications.
In addition to its versatility, a hydraulic press is surprisingly affordable and will take up little space in your new shop.
As you plan your new workshop, remember that Dake has been manufacturing metalworking equipment for over 130 years. We can help you get started with arbor presses, hydraulic presses, bandsaws, cold saws, lab presses, drill presses, custom presses, and more. We are committed to building quality products that last a lifetime.
Use our handy contact form, send us an email, or call us at 1-800-937-3253.